Complex Designs. Large-scale Results.
We partner with the largest custom low pressure structural foam molder in the country.
If you’re looking for large-scale parts, low tooling costs, cycle time optimization, weight reduction, manufacturing consistency and low production costs – structural foam molding can work for you. Structural foam allows for large part geometries, designed stiffness and weight reduction while still providing good structure, stability and durability. Low pressure structural foam allows for manufacturing flexibility in molding several parts during one press cycle.
We partner with 20/20 Custom Molded Plastics to deliver expert results. No one knows foam like 20/20, and with over 40 years of low-pressure experience, they are considered the premier custom structural foam molder in North America. 20/20 has the largest fleet of custom low-pressure machines in the industry with machines ranging from 300T to 2500T and 15 machines in the 750 to 2500T range. These machines are capable of injecting 350 pounds of plastic, creating one extra-large part up to 12 feet long. The equipment is also capable of molding 10 or more large parts during one machine cycle, with a total shot weight of 350 pounds. This multi-tool setup provides cost savings and manufacturing flexibility.
20/20 Custom Molded Plastics is ISO 9001/2015 certified.
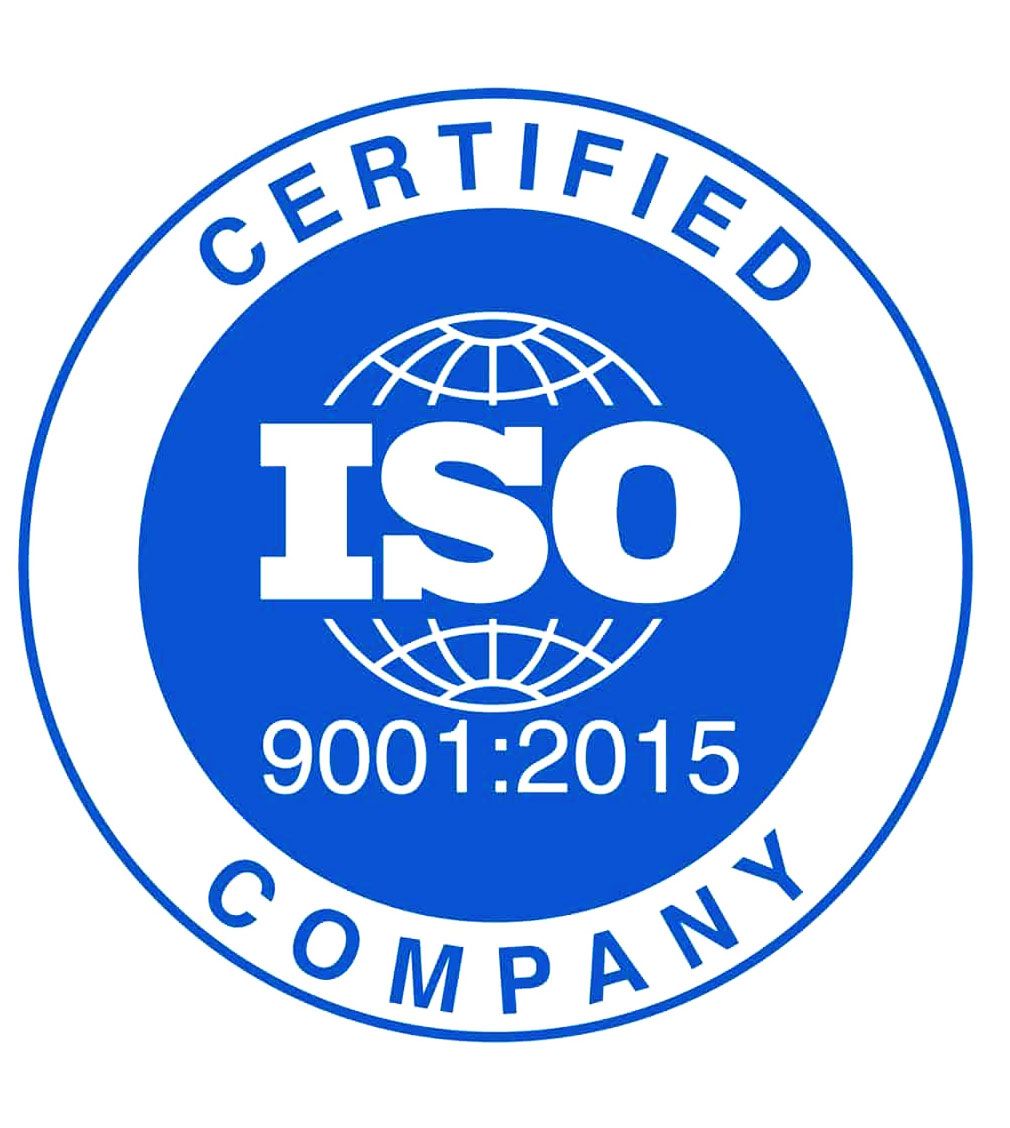